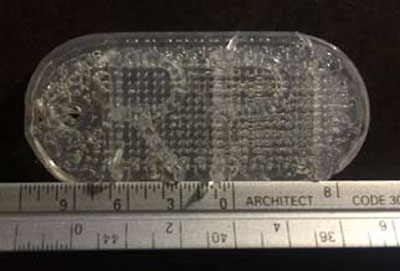
Purpose
Determine the capability of silicones in the additive manufacturing process to allow for customizable solutions in the medical, aerospace, automotive, electronic, and consumer industries. Expand the market for Momentive silicones.
Objectives
- Incorporate UV light into the print system and determine the kinetics of curing with the UV light.
- Validate that UV LSR can be used in the direct writing process.
- Test geometrical and mechanical properties of RTV and UV LSR samples.
- Determine write speed and syringe pressure for various sized syringe tips.
- Print RPI keychains using UV LSR.
Material
- Viscosity
- Power law relationship
- η = m
n-1, n and ma are material constants
- Mass flow rate: w = (ΔPR/2mL)1/n
- Frictional effects neglected in the model
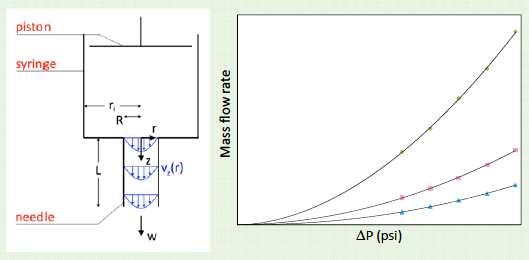
Equipment
- Pneumatic system, limited pressure
- UV light and cable mount
- Tack free time tests
- Spot cure time tests
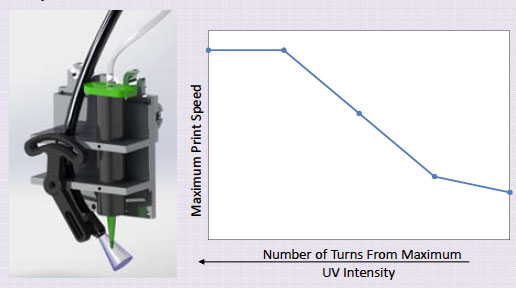
- Enclosure for 3D printer
Software
- CAD model of part
- Slic3r
- Modification of G code
- Bead‐to‐bead spacing
- Z‐height
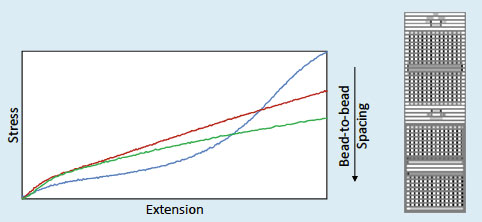
- Delays and z‐lifts to reduce stringing
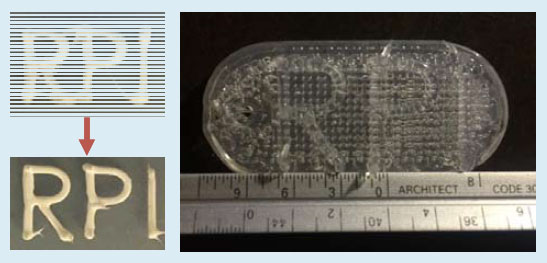
Recommendations and Future Work
- Implement external control of the UV source
- Use a lower viscosity or shear thinning silicone
- Print with higher resolution and speed
- Implement a second extrusion for support material
- Determine homogeneity of mixed material
- Sell base and catalyst in separate cartridges which mix upon extrusion
Research Area
Manufacturing, Automation, and Control
Project Type
Manufacturing
Research
Funding Agency/Sponsor
Momentive