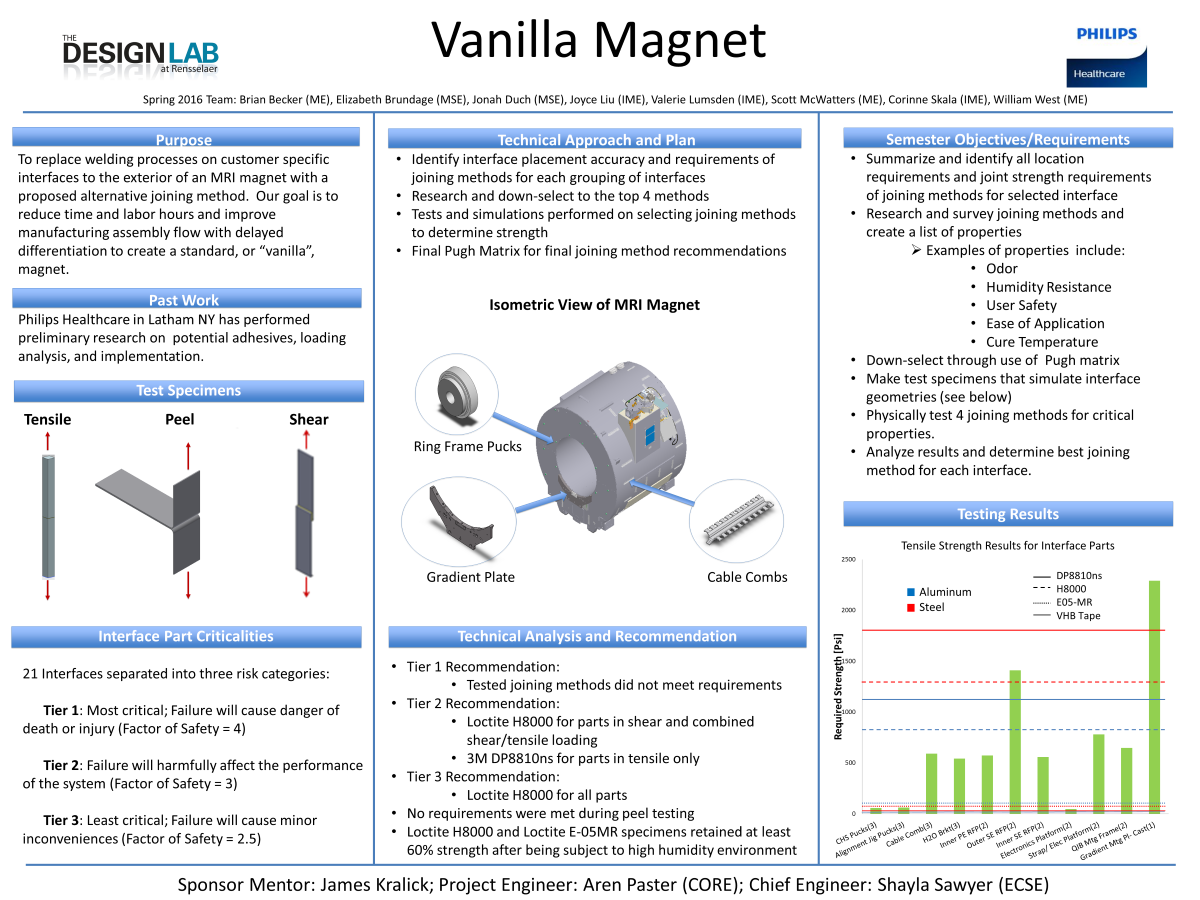
Purpose and Objective
To replace welding processes on customer specific interfaces to the exterior of an MRI magnet with a proposed alternative joining method. Our goal is to reduce time and labor hours and improve manufacturing assembly flow with delayed differentiation to create a standard, or “vanilla”, magnet which is then differentiated later in its manufacturing process
• Summarize and identify all location requirements and joint strength requirements of joining methods for selected interface
• Research and survey joining methods and create a list of properties
• Down-select through use of Pugh matrix
• Make test specimens that simulate interface geometries (see below)
• Physically test 4 joining methods for critical properties.
• Analyze results and determine best joining method for each interface.
Technical Approach
21 Interfaces separated into three risk categories:
Tier 1: Most critical; Failure will cause danger of death or injury (Factor of Safety = 4)
Tier 2: Failure will harmfully affect the performance of the system (Factor of Safety = 3)
Tier 3: Least critical; Failure will cause minor inconveniences (Factor of Safety = 2.5)
Identify interface placement accuracy and requirements of joining methods for each grouping of interfaces
• Research and down-select to the top 4 methods
• Tests and simulations performed on selecting joining methods to determine strength
• Final Pugh Matrix for final joining method recommendations
Accomplishments / Test Results
Tier 1 Recommendation:
• Tested joining methods did not meet requirements
Tier 2 Recommendation:
• Loctite H8000 for parts in shear and combined shear/tensile loading
• 3M DP8810ns for parts in tensile only
Tier 3 Recommendation:
• Loctite H8000 for all parts
No requirements were met during peel testing
Loctite H8000 and Loctite E-05MR specimens retained at least 60% strength after being subject to high humidity environment